︎︎︎
︎︎︎︎︎

︎
Aguahoja III
2021–2022
Cambridge, MA + San Francisco, CA

︎︎︎︎︎︎︎︎︎
︎︎︎
Aguahoja III was constructed in 2022 for display in the San Francisco Museum of Modern Art’s exhibition Nature X Humanity: Oxman Architects ︎︎︎. The structure is third in a series of prototypical towers designed to demonstrate the large-scale 3D printing of organic materials. Each structure is composed of an organic skin bound to a synthetic photopolymer skeleton and stands at 5 meters tall.
The structure’s skin is made from three of nature’s most abundant materials – cellulose, chitin, and pectin. These materials are mixed into hydrogel solutions and 3D printed at room temperature without any synthetic binding agents. By tuning the ratios of each of these components, composites can be printed that are flexible and tough like leather or strong and rigid like wood. Furthermore, just as in nature, these printed composites retain their ability to react to environmental changes in temperature and humidity.
By avoiding the use of synthetic additives and using minimally refined organic matter, the organic composites printed for Aguahoja retain their ability to be decomposed and digested by organisms, transferring the nutrients and energy within them to fuel new growth. In this way, Aguahoja aims to bridge the gap between humans and non-human ecosystems, pointing towards a future where the grown and the made unite.
Realized in collaboration with OXMAN and the Mediated Matter Group at MIT Media Lab ︎
Project Team ︎
Neri Oxman ︎︎︎, Nic Lee ︎︎︎, Felix Kraemer︎, Hannah Gazdus
Substructure Fabrication︎
Stratasys, Ltd., Stratasys Direct Manufacturing
Acknowledgements ︎
MIT Media Lab, Stratasys Ltd., Emerson Collective, GETTYLAB, Robert Wood Johnson Foundation, Stratasys Direct Manufacturing, San Francisco Museum of Modern Art
Press
Dezeen︎︎︎
The Economist ︎︎︎
︎
The structure’s skin is made from three of nature’s most abundant materials – cellulose, chitin, and pectin. These materials are mixed into hydrogel solutions and 3D printed at room temperature without any synthetic binding agents. By tuning the ratios of each of these components, composites can be printed that are flexible and tough like leather or strong and rigid like wood. Furthermore, just as in nature, these printed composites retain their ability to react to environmental changes in temperature and humidity.
By avoiding the use of synthetic additives and using minimally refined organic matter, the organic composites printed for Aguahoja retain their ability to be decomposed and digested by organisms, transferring the nutrients and energy within them to fuel new growth. In this way, Aguahoja aims to bridge the gap between humans and non-human ecosystems, pointing towards a future where the grown and the made unite.
Realized in collaboration with OXMAN and the Mediated Matter Group at MIT Media Lab ︎
Project Team ︎
Neri Oxman ︎︎︎, Nic Lee ︎︎︎, Felix Kraemer︎, Hannah Gazdus
Substructure Fabrication︎
Stratasys, Ltd., Stratasys Direct Manufacturing
Acknowledgements ︎
MIT Media Lab, Stratasys Ltd., Emerson Collective, GETTYLAB, Robert Wood Johnson Foundation, Stratasys Direct Manufacturing, San Francisco Museum of Modern Art
Press
Dezeen︎︎︎
The Economist ︎︎︎
︎
Aguahoja III demonstrates the capabilities of abundant, organic material stocks to create structural composites
︎
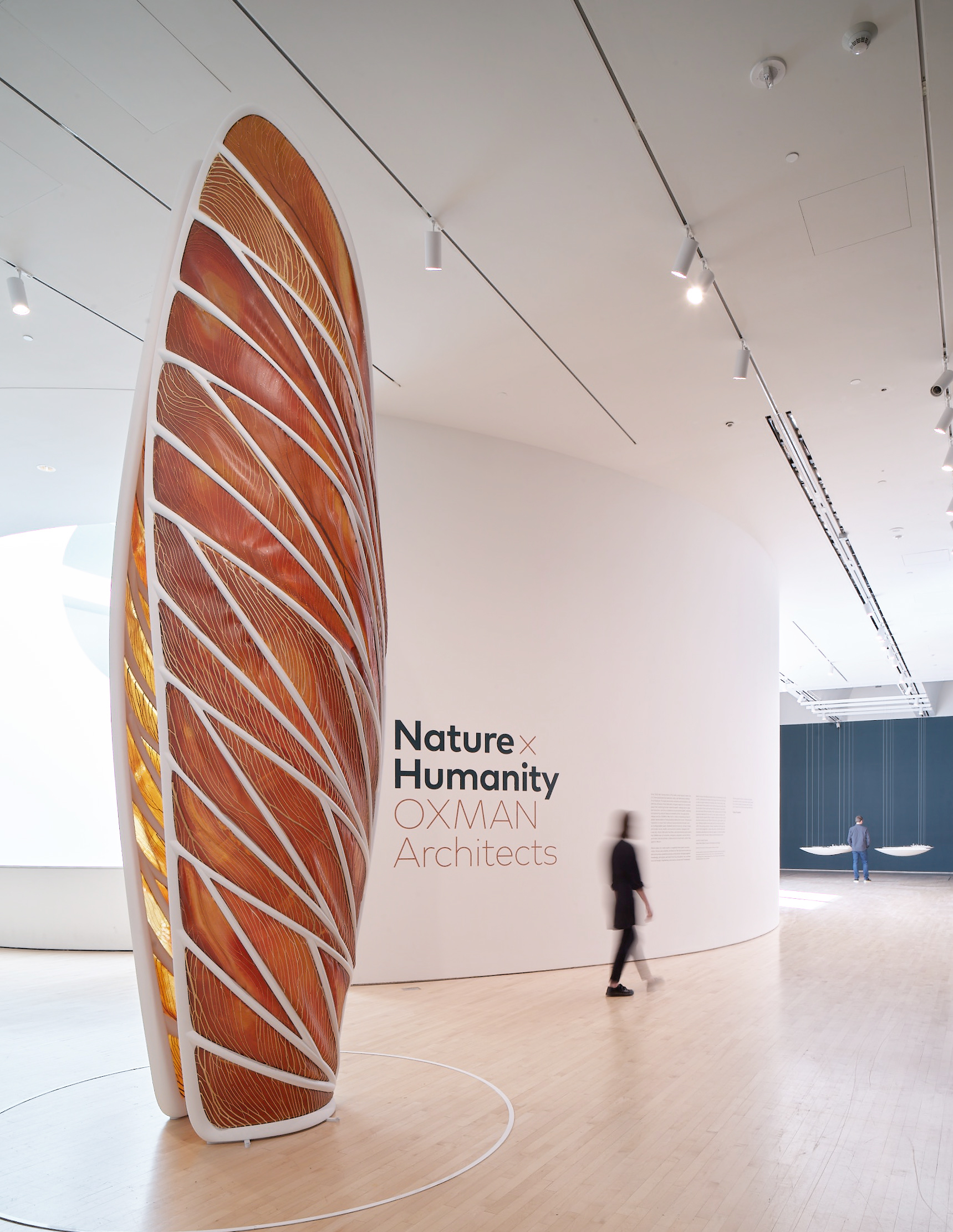

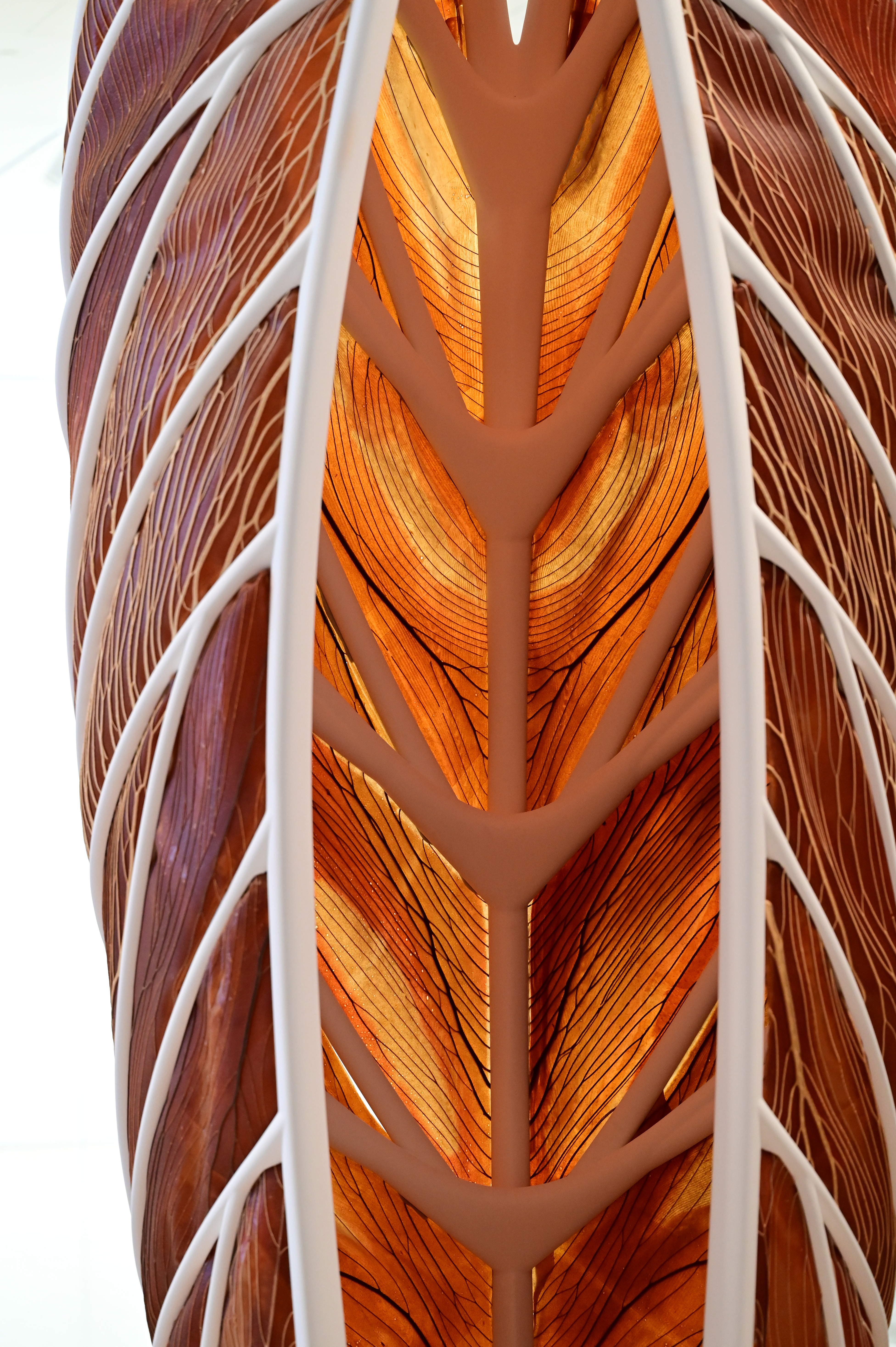
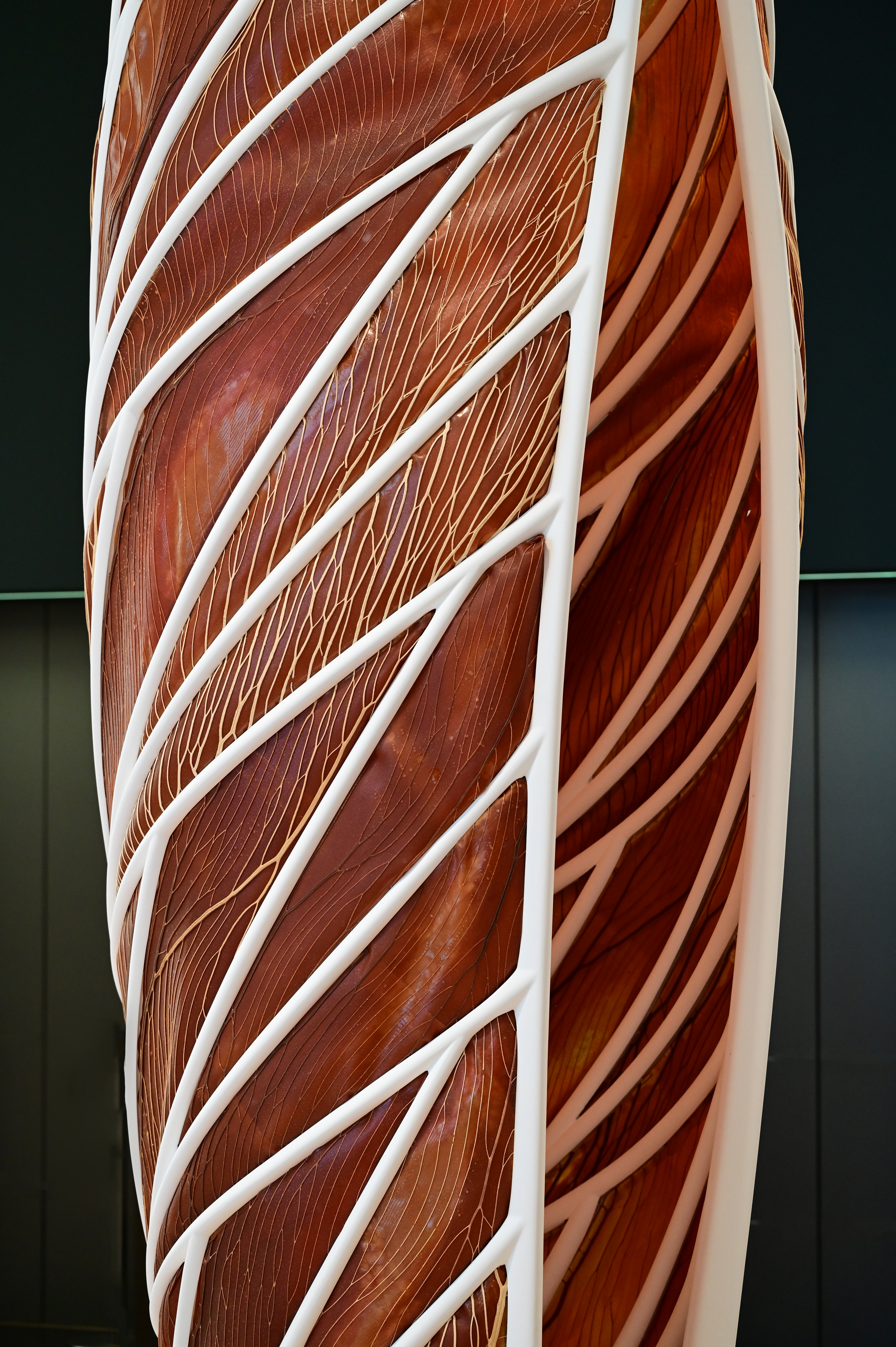
Digital Fabrication
Aguahoja III employs a generative design method that uses structural simulation to assign its distribution of materials and multi-scale geometry. This procedural design method can flexibly assign a biopolymer skin to any input geometry and automatically generate the material combinations, machine parameters, and toolpaths needed to fabricate the structure. This end-to-end pipeline for digital design and fabrication encompasses a flexible, automated system with tight coupling between environmental data, structural performance, and fabrication information.
Aguahoja III employs a generative design method that uses structural simulation to assign its distribution of materials and multi-scale geometry. This procedural design method can flexibly assign a biopolymer skin to any input geometry and automatically generate the material combinations, machine parameters, and toolpaths needed to fabricate the structure. This end-to-end pipeline for digital design and fabrication encompasses a flexible, automated system with tight coupling between environmental data, structural performance, and fabrication information.
︎︎︎︎︎
The structure’s skin is comprised of a flexible base-layer and a rigid layer of reinforced veins. Containing mostly pectin and chitosan, the base-layer of the skin allocates stiff materials in areas of high structural load and flexible materials in areas of high displacement. The veins contain anisotropic cellulose fibers and chitosan which are printed in a pattern that conforms to the gradient of structural stresses to provide maximum reinforcement in areas of high load.
The structure’s skin is comprised of a flexible base-layer and a rigid layer of reinforced veins. Containing mostly pectin and chitosan, the base-layer of the skin allocates stiff materials in areas of high structural load and flexible materials in areas of high displacement. The veins contain anisotropic cellulose fibers and chitosan which are printed in a pattern that conforms to the gradient of structural stresses to provide maximum reinforcement in areas of high load.

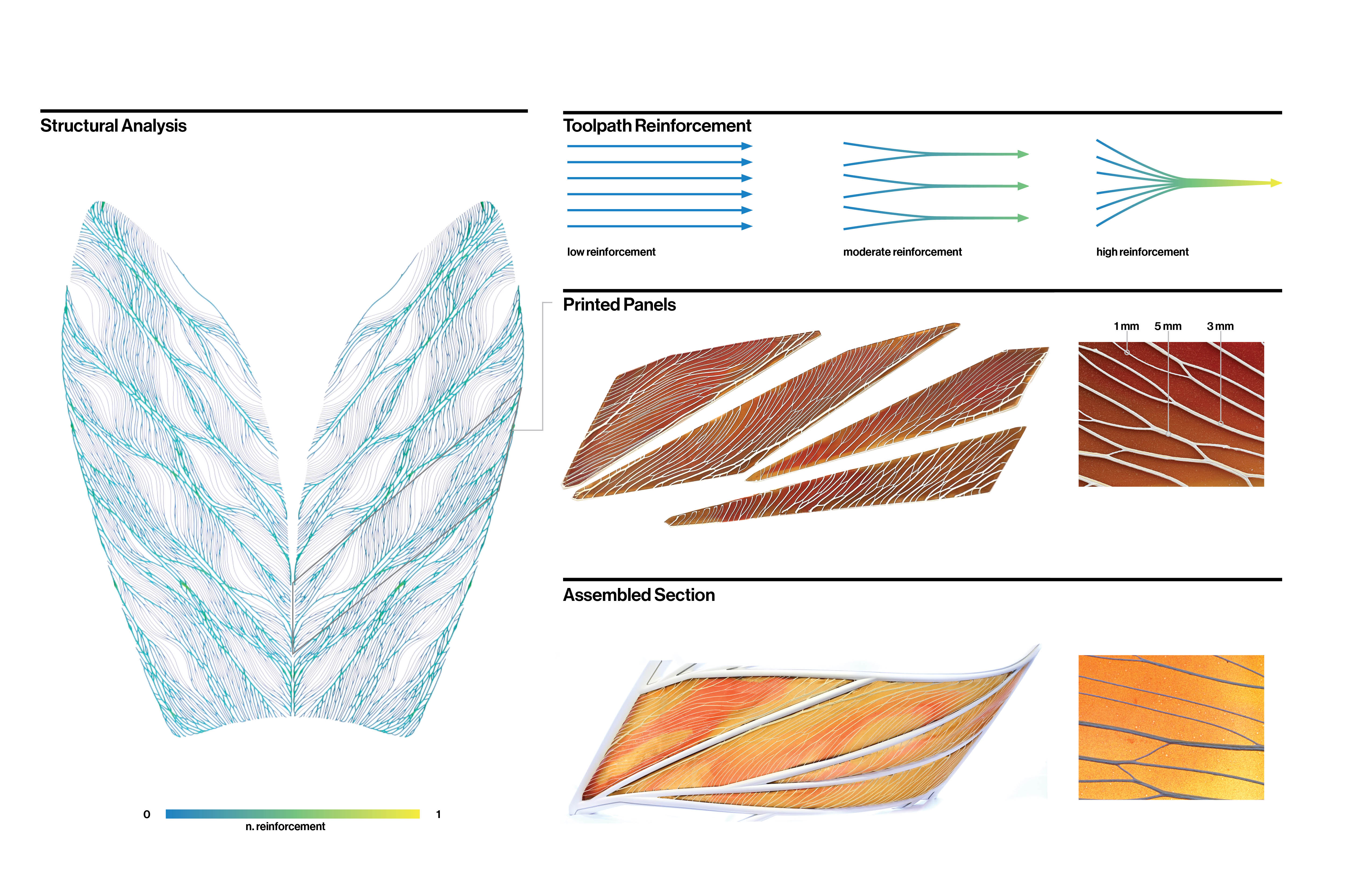

The cellulosic veins along Aguahoja III’s skin are formed through the novel method of Stress-Aligned Anisotropic Printing (SAAP). During the extrusion process, cellulose fibers are shear-thinned to form cross-linked bundles that align to the printed direction. These veins have increased tensile strength along this aligned printing direction. By aggregating multiple groups of veins into thickened bundles, the degree of reinforcement along these paths can be enhanced.
In contrast to conventional 3D printing, Aguahoja’s materials are printed in a semi-liquid state in which there is a high degree of cross-linking between adjacent paths. This leads to the formation of tightly bonded branches which behave as a single monolithic object where multiple paths come together.
Through the use of SAAP, Aguahoja III enables the creation of rigid structural composites with enhanced strength and directed anisotropy from a pallet of sustainable, abundant materials.
Materials
︎︎︎︎︎︎︎︎︎︎︎︎︎︎︎︎
︎
Pavilion
2019–2020
Cambridge, MA + Abano Terme, IT + New York, NY
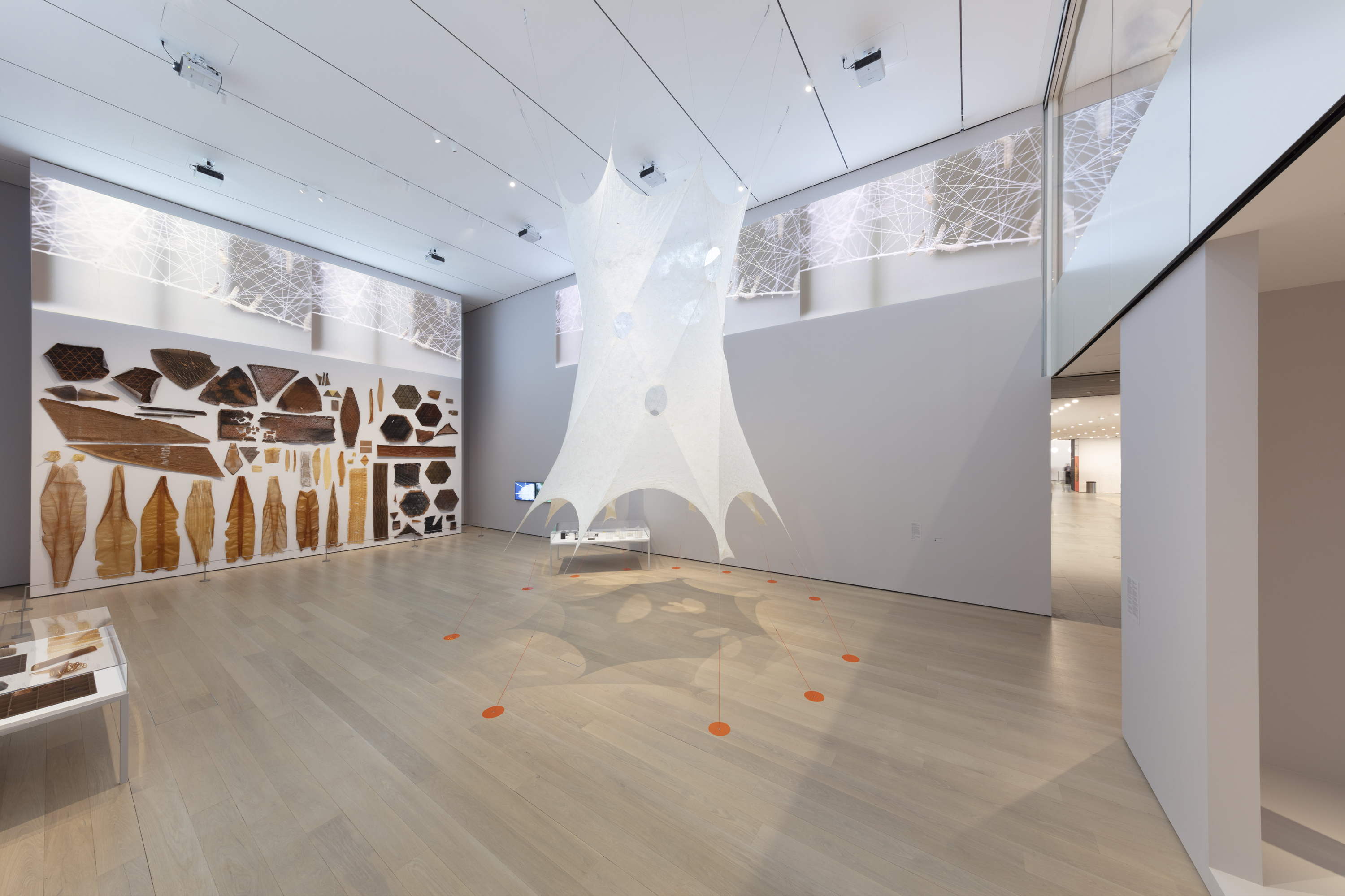
“Digital Image © 2020 The Museum of Modern Art, New York.” Photographed by Denis Doorly
Commissioned for the exhibition Neri Oxman: Material Ecology︎ at the Museum of Modern Art, New York, in 2020, Silk Pavilion II stands at six meters tall and five meters wide. Building on research developed for Silk Pavilion I ︎, this successor project tackled challenges associated with scale and sericulture.
The project utilizes an integrated kinetic mandrel designed to guide the natural spinning motion of the silkworms through clockwise rotation, fusing technology and biology to unite the woven and the spun.
Realized as part of research project conducted in the Mediated Matter Group at MIT Media Lab ︎
Research Team ︎
João Costa, Christoph Bader︎ , Sunanda Sharma︎, Felix Kraemer︎, Susan Williams︎, Jean Disset︎ and Neri Oxman ︎ Undergraduate researcher: Sara Wilson
Contributors ︎
Davide Biasetto, Il Brolo Società Agricola SRL, Padua; Levi Cai; Silvia Cappellozza and Alessio Saviane, Council for Agricultural Research and Agricultural Economics Analysis (CREA-AA), Bologna; Natalia Casas; Kelly Egorova; Fiorenzo Omenetto, Tufts University; Sol Schade, Advanced Functional Fabrics of America (AFFOA); James Weaver, Wyss Institute, Harvard University; Nitzan Zilberman; Bodino; Front Inc.; MIT Media Lab
︎
The project utilizes an integrated kinetic mandrel designed to guide the natural spinning motion of the silkworms through clockwise rotation, fusing technology and biology to unite the woven and the spun.
Realized as part of research project conducted in the Mediated Matter Group at MIT Media Lab ︎
Research Team ︎
João Costa, Christoph Bader︎ , Sunanda Sharma︎, Felix Kraemer︎, Susan Williams︎, Jean Disset︎ and Neri Oxman ︎ Undergraduate researcher: Sara Wilson
Contributors ︎
Davide Biasetto, Il Brolo Società Agricola SRL, Padua; Levi Cai; Silvia Cappellozza and Alessio Saviane, Council for Agricultural Research and Agricultural Economics Analysis (CREA-AA), Bologna; Natalia Casas; Kelly Egorova; Fiorenzo Omenetto, Tufts University; Sol Schade, Advanced Functional Fabrics of America (AFFOA); James Weaver, Wyss Institute, Harvard University; Nitzan Zilberman; Bodino; Front Inc.; MIT Media Lab
︎
In a departure from Silk Pavilion I, this structure is comprised of three interrelated layers. Its innermost primary structure is made of one-dimensional, braided steel wire ropes, while the secondary structure is a two-dimensional knit fabric onto which silkworms are positioned. The outermost layer is a three-dimensional structure biologically spun with the help of some 17,000 silkworms sourced in the Veneto region of Italy where the tradition of sericulture and silk manufacturing has been a part of its history since 12th century Renaissance.
Over the course of 10 days, the silkworms spun horizontally across the base structures. As they progressed, a rotating mechanism guided their spinning motions upwards. The resulting density of the silk layer–influenced by change in light and heat–varies across the structure. The holes in the knit layer, created as a result of the interaction with silkworm excrement, are strategically placed to release tensile stress.
Over the course of 10 days, the silkworms spun horizontally across the base structures. As they progressed, a rotating mechanism guided their spinning motions upwards. The resulting density of the silk layer–influenced by change in light and heat–varies across the structure. The holes in the knit layer, created as a result of the interaction with silkworm excrement, are strategically placed to release tensile stress.

︎︎︎︎︎
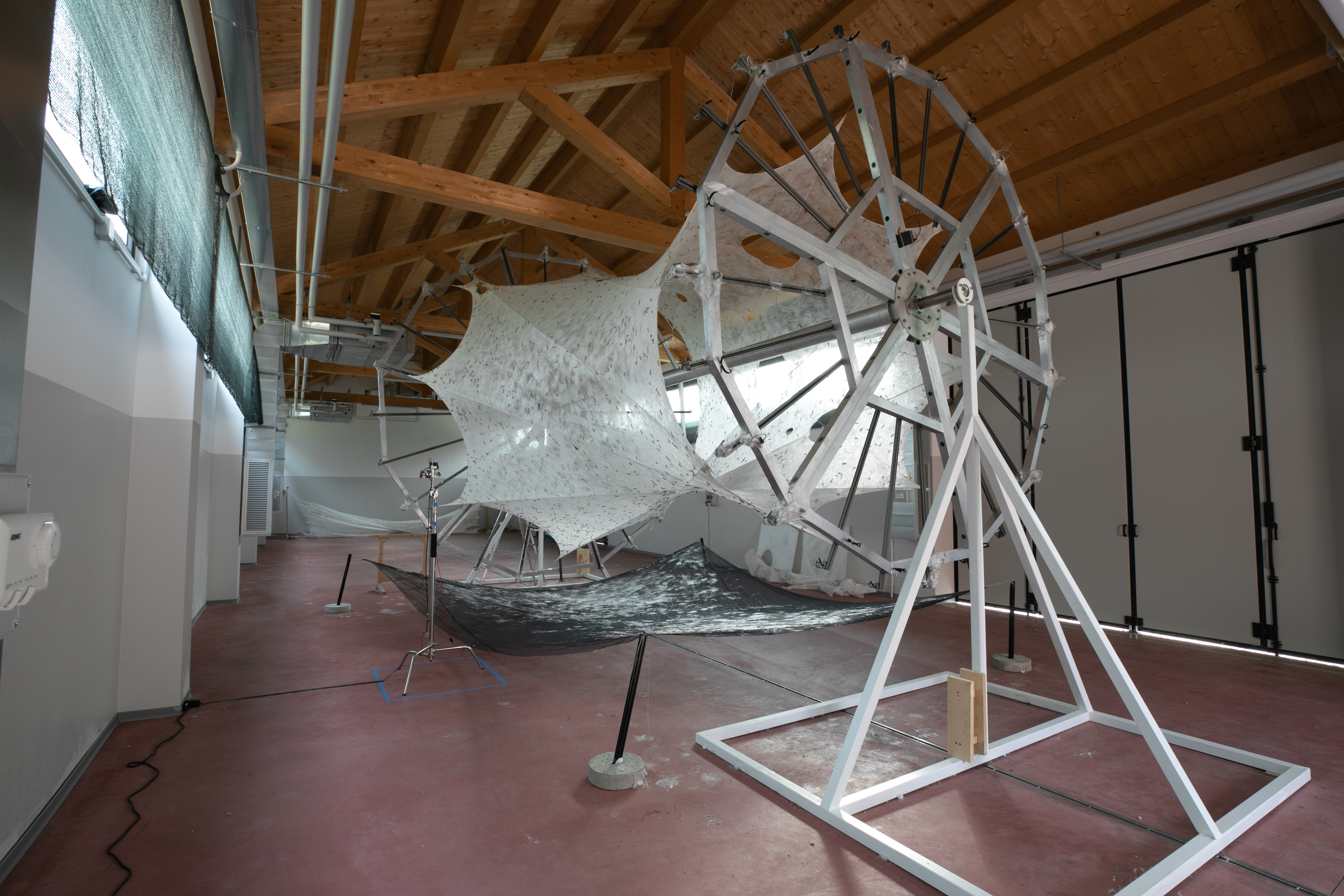
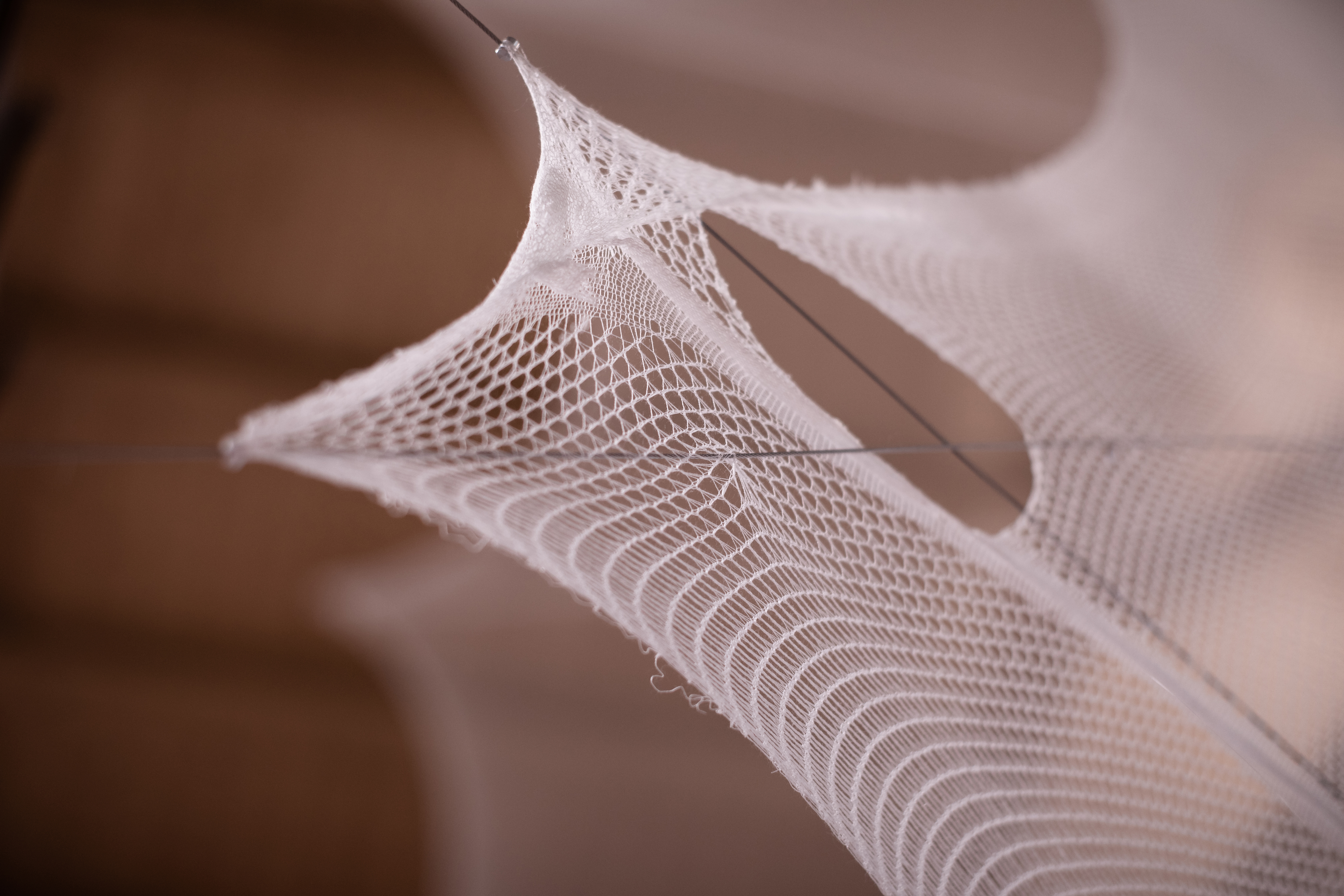

︎︎︎

︎︎︎︎︎︎︎︎︎︎︎︎
A scanning mechanism was set up in order to allow for tracking of structural changes over the course of production. The system encompasses a Lidar scanner working in tandem with a rotary encoder and prepared DC motor to create a point cloud data.
As the traditional process of harvesting silk from the cocoon kills the larva, sericulture has been criticized by animal welfare and rights activists. In the textile and silk industry today, silkworms are exterminated while in their cocoon, dissolving the adhesive that glues one strand of silk to the layers below. This process allows a single silk strand to be unrolled from the cocoon but disrupts the life cycle and development of the organism. As the Silk Pavilion demonstrates, structures can influence silkworms to spin in sheets instead of cocoons.
The project illustrates how these compact and unique insects can act not only as living looms but as co-designers uniting with humans to design and construct architectural-scale structures embodying co-fabrication for cohabitation.
︎︎
︎︎︎
︎︎︎︎︎︎
︎

︎︎︎︎︎︎︎︎︎︎︎︎︎︎︎︎
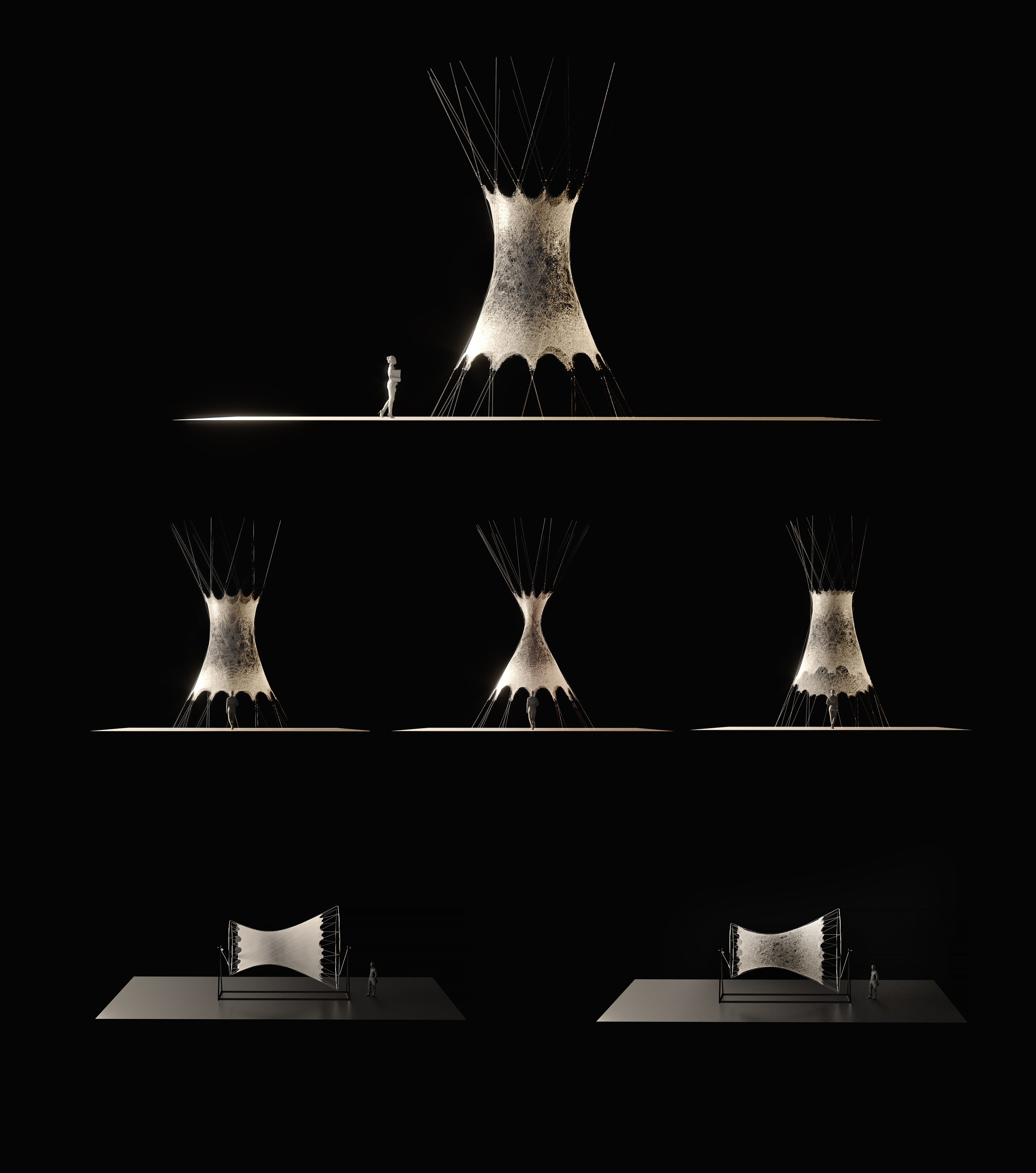

︎
Tools
2017 –
Cambridge, MA
Realized as part of research conducted in the Mediated Matter Group at MIT Media Lab ︎
Along the research process that culminated with the Silk Pavilion, various tools were designed and produced. Each had to perform a different task to work with fabrication systems and the silkworms.
Here is a selection of these tools.
Research Team ︎
João Costa, Christoph Bader︎ , Sunanda Sharma︎, Felix Kraemer︎, Susan Williams︎, Jean Disset︎ and Neri Oxman ︎
︎
Along the research process that culminated with the Silk Pavilion, various tools were designed and produced. Each had to perform a different task to work with fabrication systems and the silkworms.
Here is a selection of these tools.
Research Team ︎
João Costa, Christoph Bader︎ , Sunanda Sharma︎, Felix Kraemer︎, Susan Williams︎, Jean Disset︎ and Neri Oxman ︎
︎
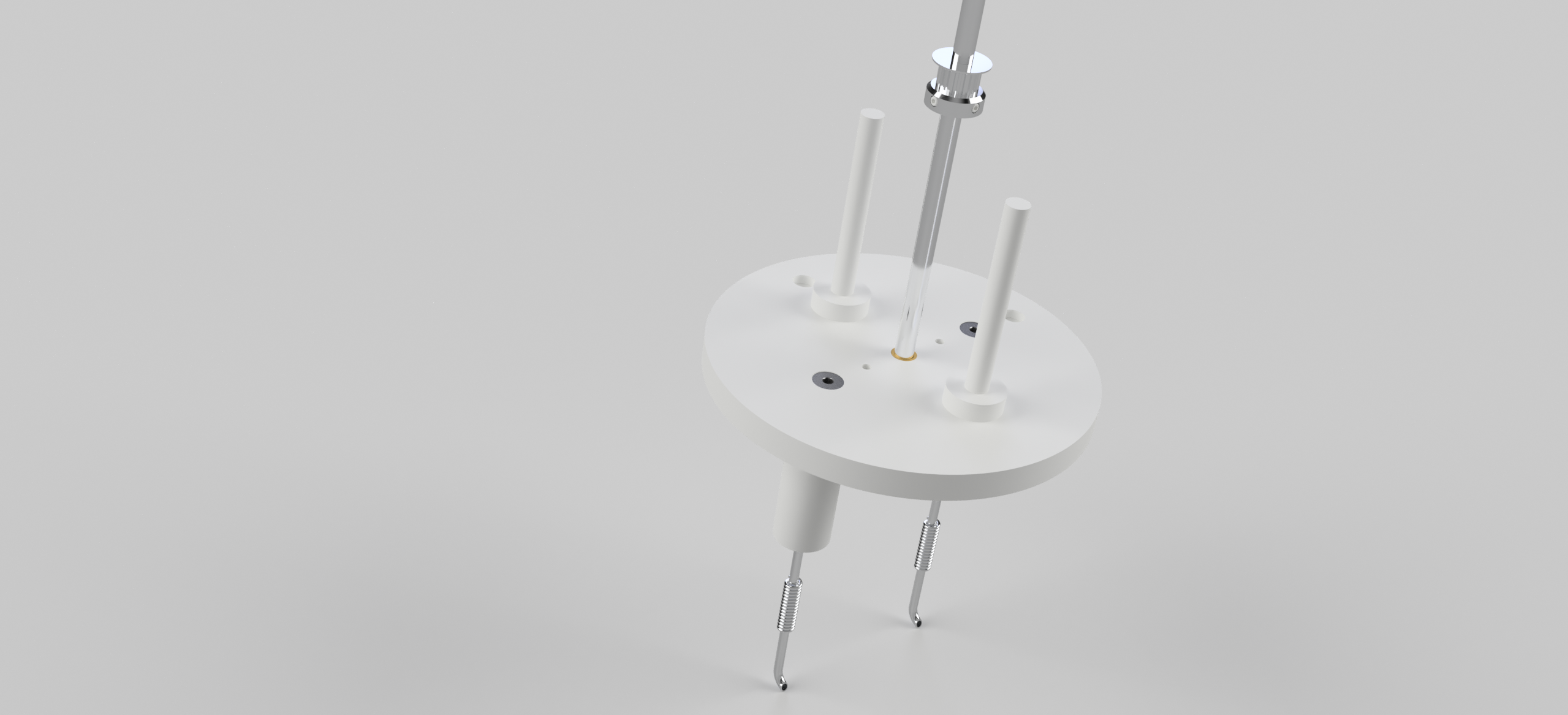
End Effectors for thread deposition ︎
︎
︎
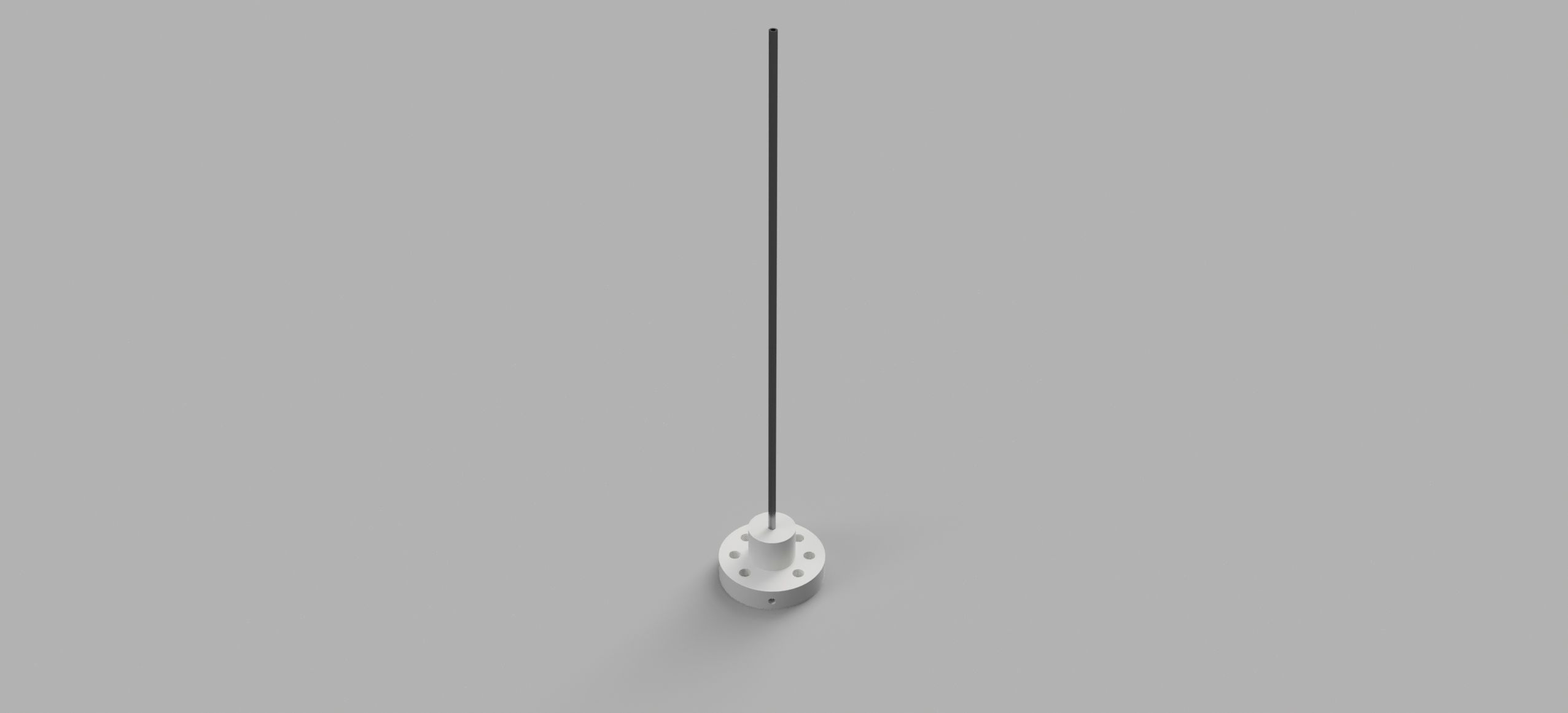
︎
︎

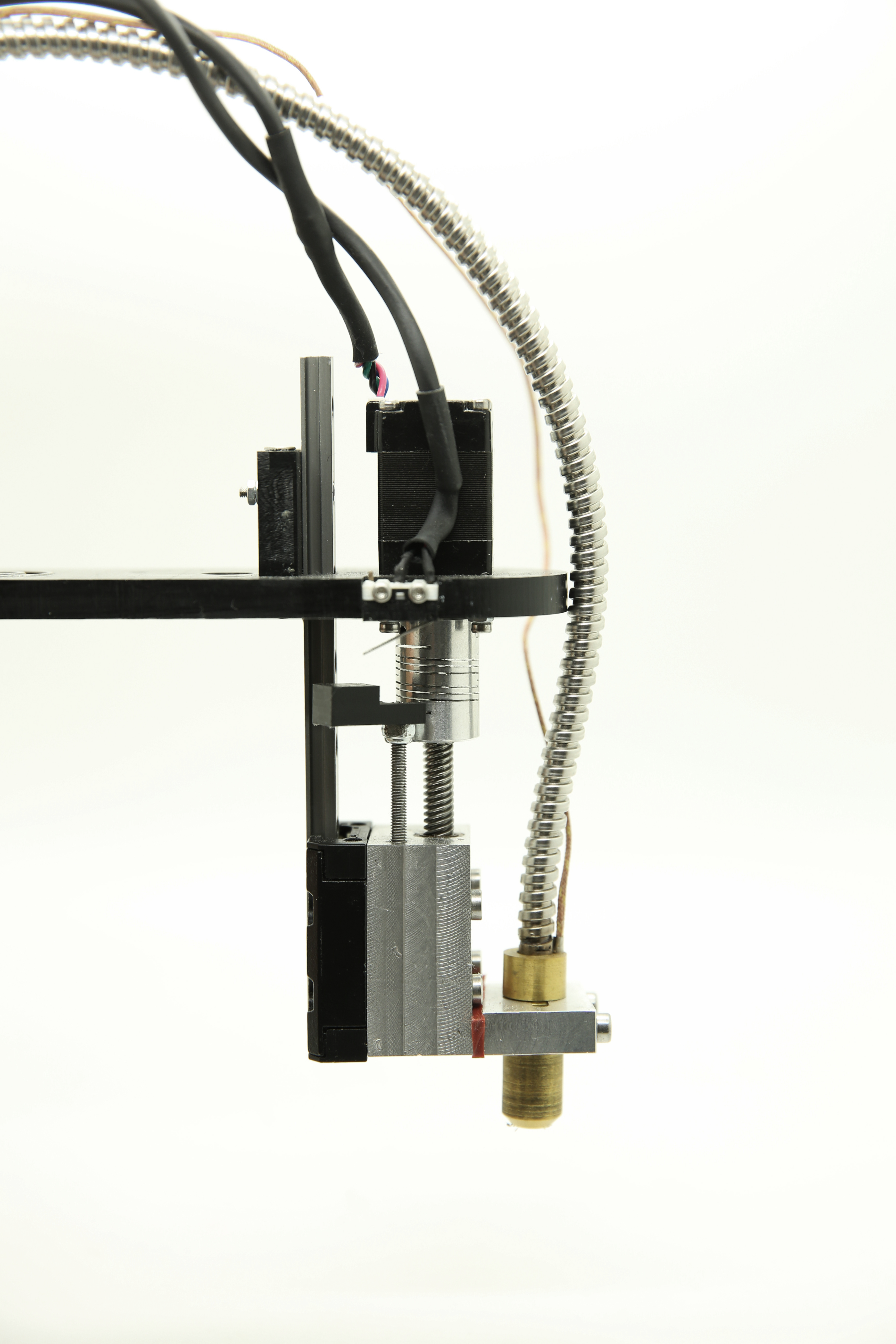
︎︎︎︎︎︎︎
![]()
︎︎︎︎︎︎︎︎︎︎︎︎︎︎

︎︎︎︎︎︎︎︎︎︎︎︎︎︎

︎
Studies
2017 –
Cambridge, MA
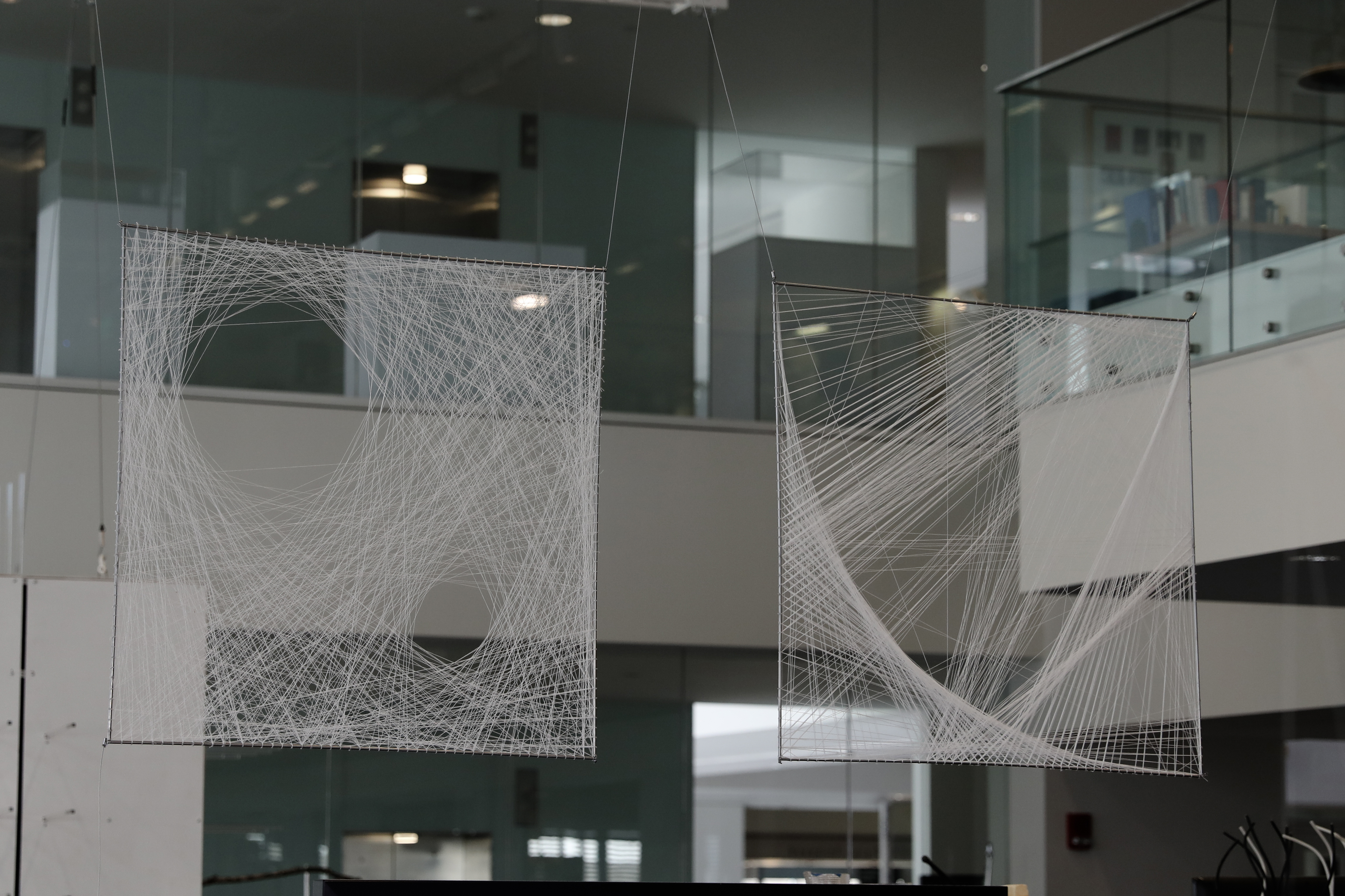
Realized as part of research conducted in the Mediated Matter Group at MIT Media Lab ︎
A selection of studies done for the development of the Silk Pavilion. These include processes and investigative experiments that look into new forms of fabricating thread-based structures and the required mechanisms.
Research Team ︎
João Costa, Christoph Bader︎ , Sunanda Sharma︎, Felix Kraemer︎, Susan Williams︎, Jean Disset︎ and Neri Oxman ︎
︎
A selection of studies done for the development of the Silk Pavilion. These include processes and investigative experiments that look into new forms of fabricating thread-based structures and the required mechanisms.
Research Team ︎
João Costa, Christoph Bader︎ , Sunanda Sharma︎, Felix Kraemer︎, Susan Williams︎, Jean Disset︎ and Neri Oxman ︎
︎
︎
Frames constructed for the Broken Nature exhibition at the Trienale di Milano in 2019. Thread was deposited by a CNC machine including custom tools and controls.
Frames constructed for the Broken Nature exhibition at the Trienale di Milano in 2019. Thread was deposited by a CNC machine including custom tools and controls.


︎︎︎︎︎︎︎︎︎︎︎︎︎︎
Experiments with the Bombyx mori silkworm looking into different stimuli and their effect on silk deposition and construction of the cocoon structure.
Experiments with the Bombyx mori silkworm looking into different stimuli and their effect on silk deposition and construction of the cocoon structure.
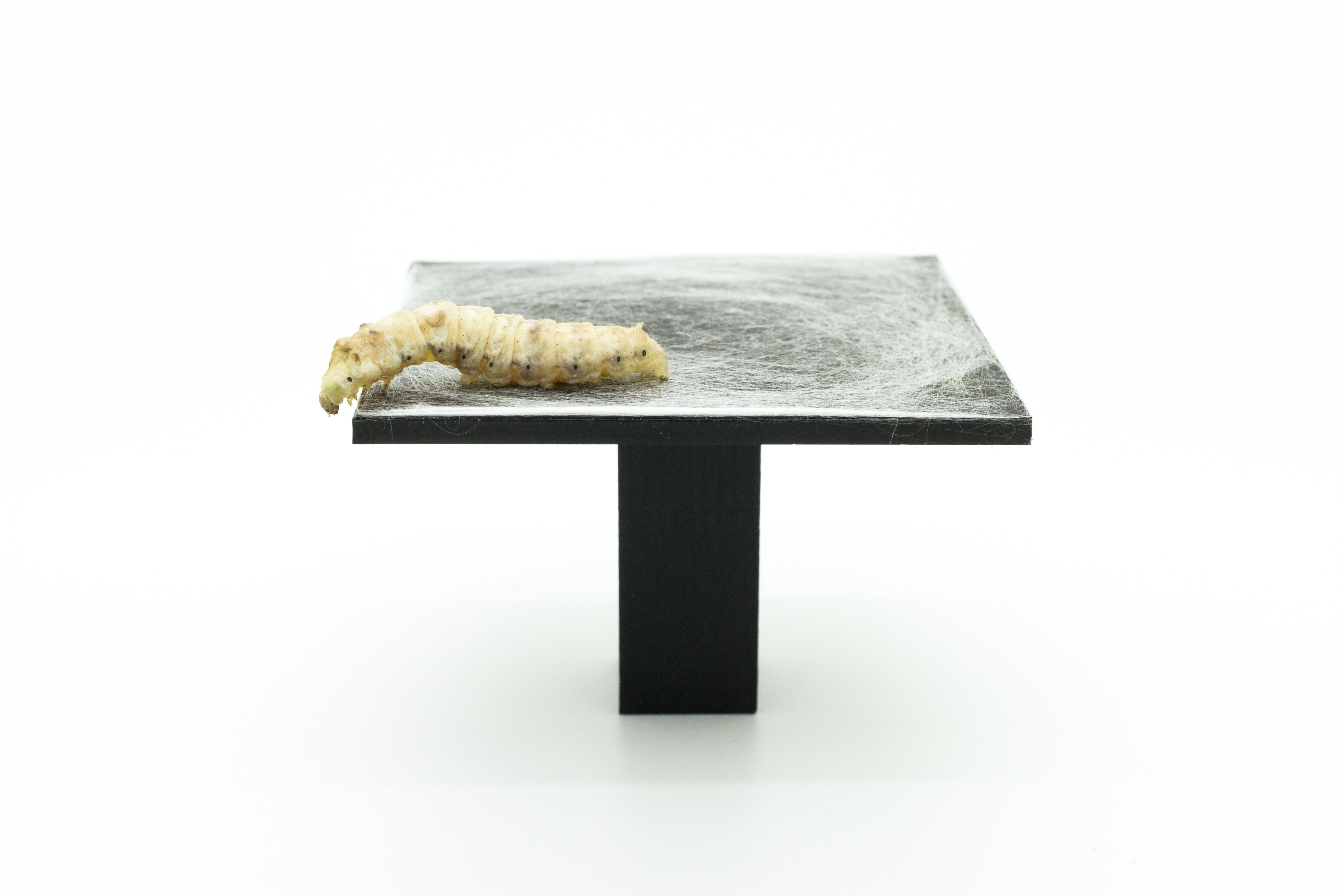
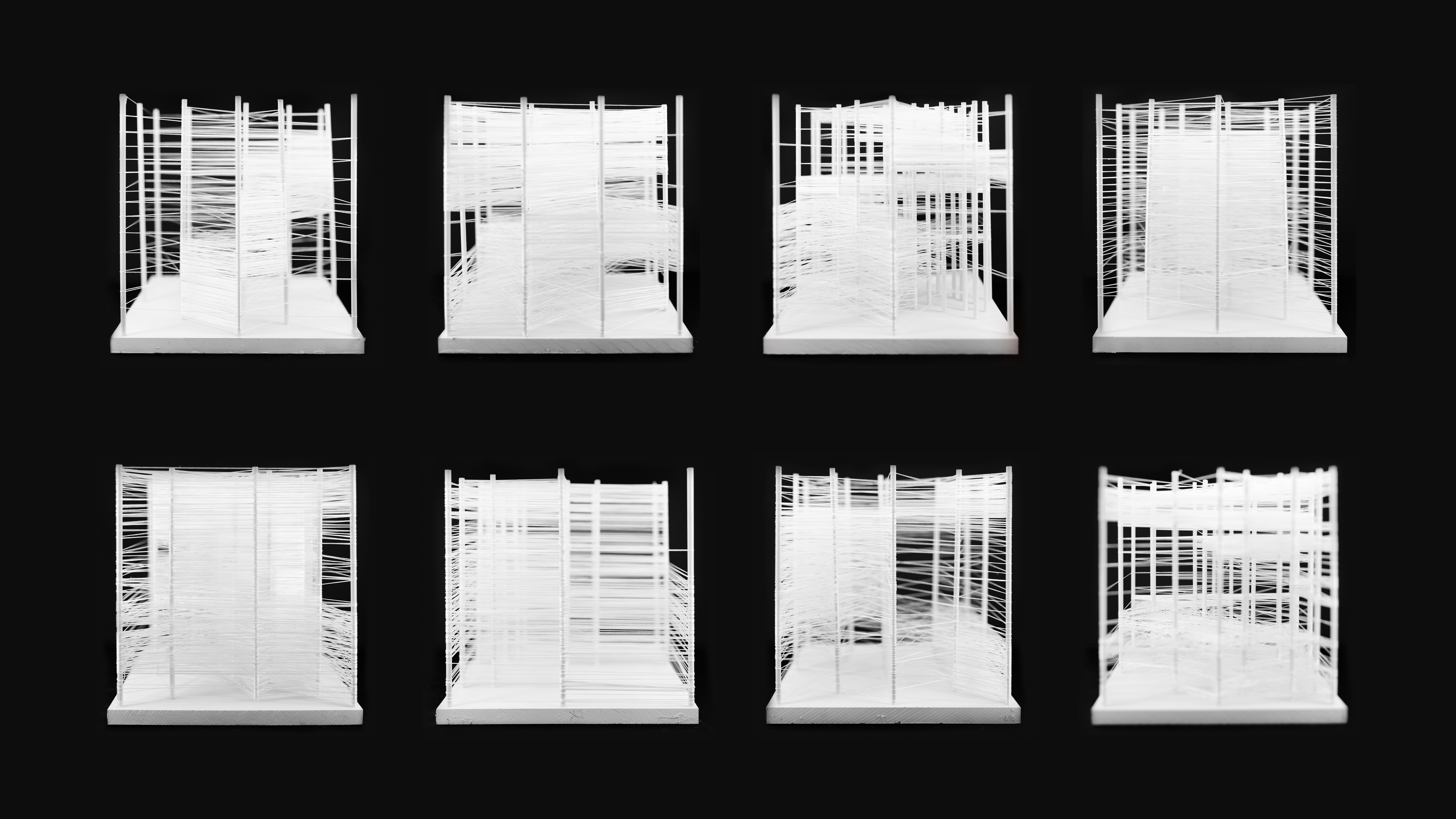
6”x6”x6” CUBES
︎︎︎︎︎
Investigation of three-dimensional thread-based structures. Here are some models that present different distribution of density within structures constrained by the boundaries of a cube.
The structures were built by a robotic arm and a CNC machine and consisted of a single silk thread. The toolpath and tools for achieving these results were all part of the research process and can be seen in the figures.
Investigation of three-dimensional thread-based structures. Here are some models that present different distribution of density within structures constrained by the boundaries of a cube.
The structures were built by a robotic arm and a CNC machine and consisted of a single silk thread. The toolpath and tools for achieving these results were all part of the research process and can be seen in the figures.


︎
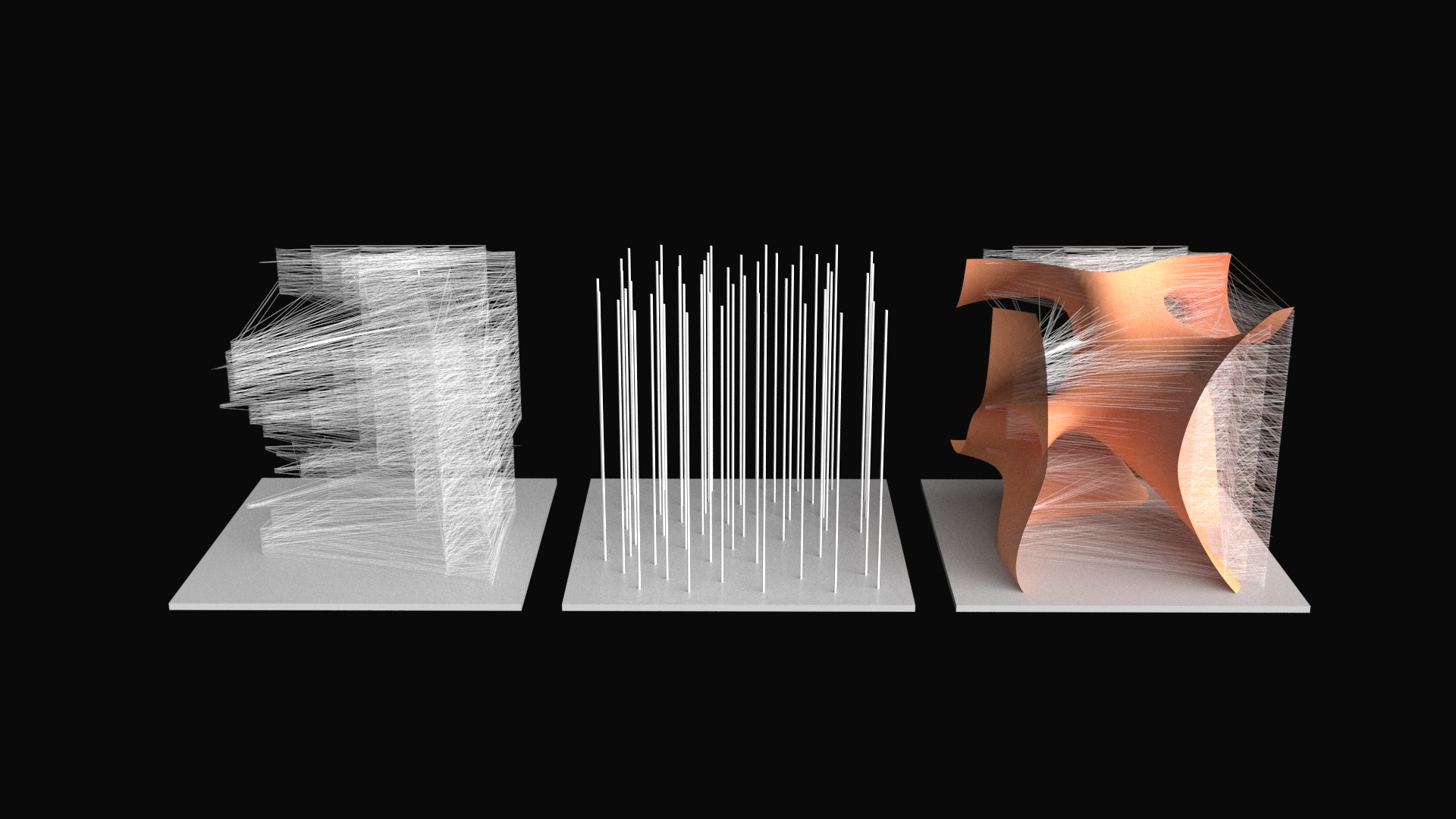
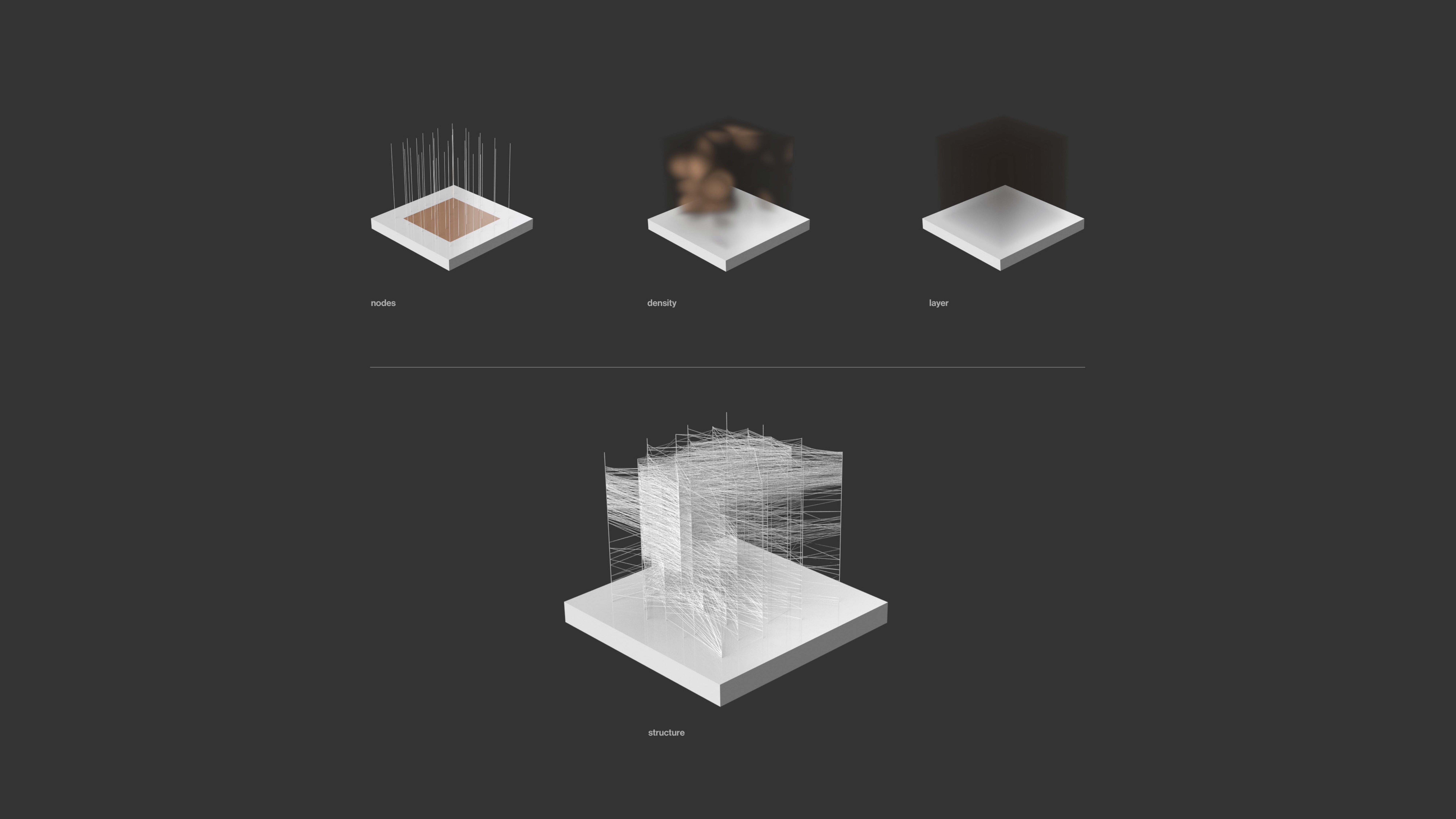
FIBER DENSITY DISTRIBUTION
︎

︎︎︎︎
︎︎
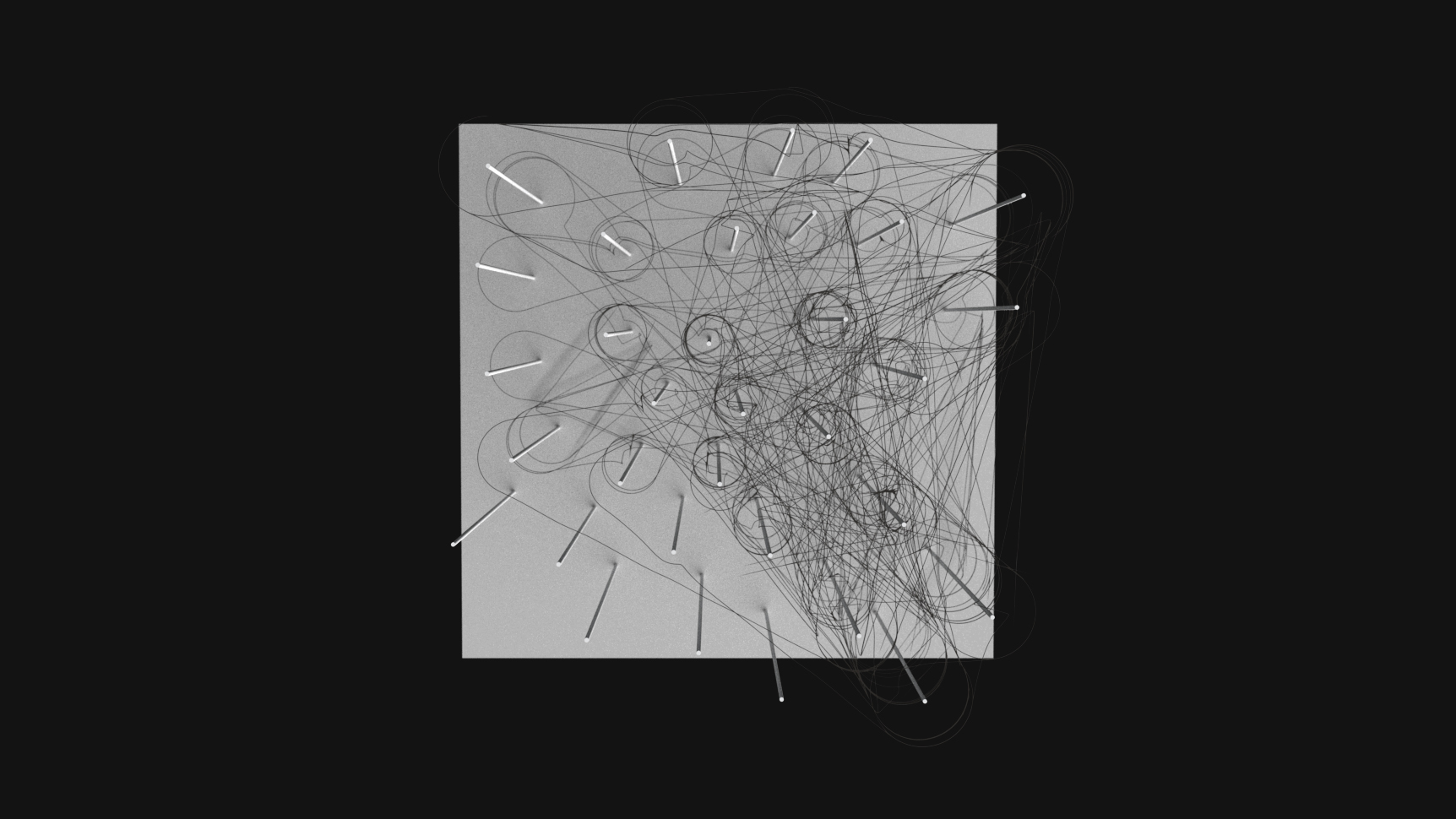
Top view of the toolpath developed for achieving thread deposition. A custom script was created in order to avoid collision between the poles and the end-effector.
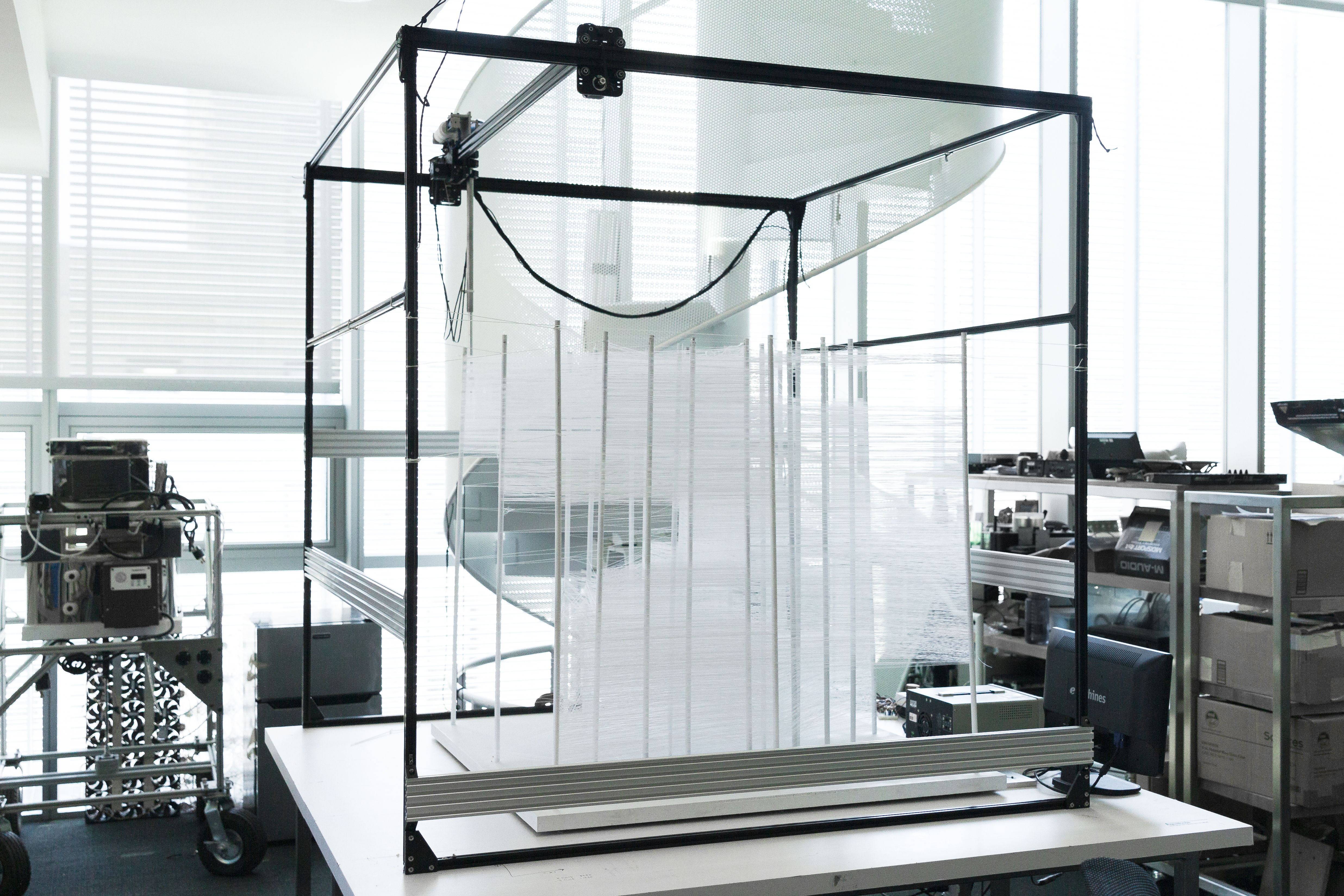
︎
1.5mx1.5mx1.5m
Gantry

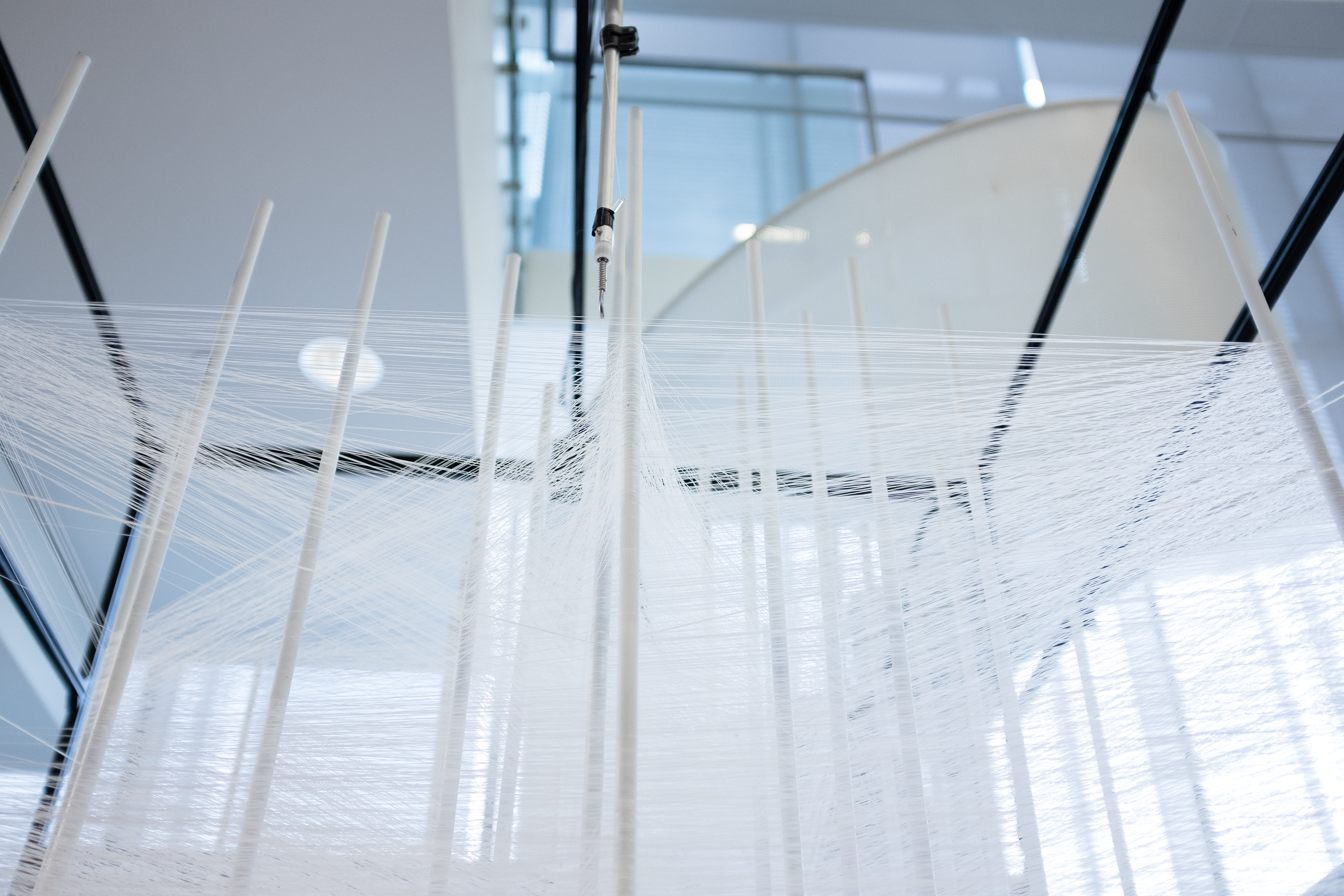
︎